Ten Years of ContiLifeCycle Plant in Stöcken, Hanover
- ContiLifeCycle plant: Combination of retreading and rubber recycling plant
- Retreaded truck tires provide efficiency and sustainability
- Continental aims to recover 60 percent of the materials used in tire construction from tires by 2050 at the latest
Hanover, November 20, 2023. The ContiLifeCycle plant in Stöcken, Hanover (Germany), is celebrating its tenth anniversary today. The first truck tire was retreaded at the new ContiLifeCycle plant in Stöcken, Hanover, in November 2013. A further 900,000 truck and bus tires have been processed over the past ten years. Hot retreading extends the service life of truck and bus tires by renewing their treads and sidewalls. According to a study by the Fraunhofer Institute for Environmental, Safety and Energy Technology (UMSICHT), the CO2 emissions of retreaded tires can be as much as roughly 50 percent lower than those of comparable new tires. The amount of recycled and renewable materials in retreaded tires can be up to 85 percent.
Felix Hantelmann, Head of the ContiLifeCycle plant in Stöcken, Hanover, congratulated the employees at the anniversary celebration: "This anniversary is not only proof of ten years of premium quality but also of our active, progressive, and innovative approach to sustainability. I would like to thank the entire team for its great dedication and support." In honor of the anniversary, Continental is planning various activities for November 20 to celebrate the ContiLifeCycle plant's birthday. After an in-house ceremony, family members will also be invited to join.
The ContiLifeCycle plant in Stöcken combines a state-of-the-art retreading facility for bus and truck tires with its own industrial-scale rubber recycling plant. In addition to retreading truck and bus tires, Continental has developed a process for devulcanization of vulcanized rubber compounds. The resulting rubber recyclate is of a particularly high quality, meaning it can be reused for new tire compounds. Since the recycling plant started operating, roughly 10,000 metric tons of material have gone into new mixtures; this material would have gone to waste without the recycling process. The ContiLifeCycle plant has thus been making a contribution to greater sustainability in the tire industry ever since it went into operation.
Expanding the circular economy
The production of retreaded truck and bus tires, which have product characteristics comparable to those of new tires, is firmly enshrined in Continental's ambitious sustainability strategy. Continental is working tirelessly to advance innovative technologies and sustainable products and services throughout its entire value chain, from sourcing sustainable materials to recycling old tires. The aim is to recover 60 percent of the materials used in tire construction from tires by 2050 at the latest.
Retreaded tires also contribute to Continental's Lowest Overall Driving Costs (LODC) concept, which is specially designed for vehicle fleets. The LODC concept is a holistic consulting approach that helps fleet customers to reduce their operating costs that relate to tires. Thanks to retreaded tires, Continental's fleet customers have an effective portfolio of solutions for efficient and sustainable fleet operation at their disposal.
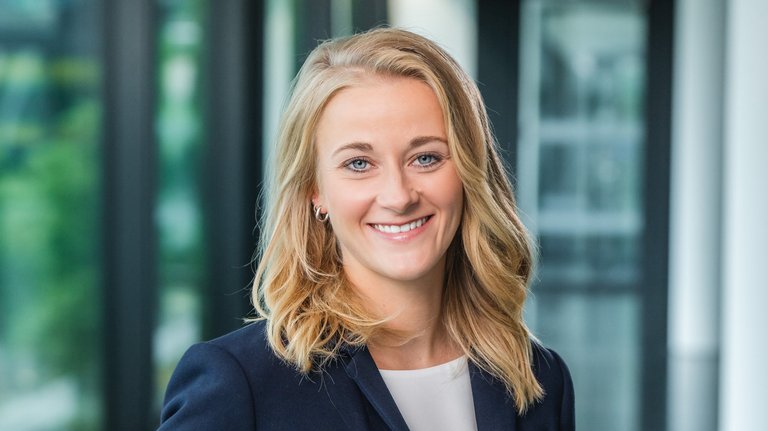
Laura Averbeck
Manager Communications Sustainability
Continental Tires