Conti Professional Simplifies Design of Belt Drives
- In “Conti Professional”, Continental offers a design program for two- and multi-pulley drives. The web-based application can be run in a browser to calculate drives using open-ended or endless belts, with the number of pulleys user-definable between two and 20. So much for the theory – but how does Conti Professional work in practice?
To answer that question, an oil pump drive will be designed by way of an example with the aid of Conti Professional. “The data used has been selected to clearly illustrate the working process with the software,” says Marcel Vogel, an application engineer who played a key role in the development of the software. He is also responsible for continuing development and the addition of new features.
Create a new project
After the mandatory registration and login, the user is shown a dashboard. In the project overview, s/he can call up stored calculations. Clicking on “Create Project” opens a dialog box in which the user can enter the project name, company name and notes on the drive to be designed. S/he can also define the project variant, for example if the drive is to be designed in various output classes.
Once this data has been saved, a project editor opens in the browser. Under “Type of System”, the user first specifies whether the drive is to use open-ended or endless belts. Next, various parameters can be defined under “Belt Selection”, as a result of which the selection is gradually narrowed down. If, for instance, the user selects “Timing belt” under “Belt nature” and “Double-sided profile section” as the property required for the oil pump drive, s/he can choose from three belt types. Since the oil pump is to be particularly powerful, the user opts for the Synchrotwin CXP, the most powerful double-sided rubber timing belt in the product range. The software then adds the tooth profile DHTD and the pitch D8M.
Calculate and visualize
Once the belt has been selected, the user can input the oil pump drive’s geometry data into Conti Professional, ranging from the number of pulleys to the position of the belt tensioner through to the data for the individual pulleys. In our example, the drive to be designed is to have three pulleys, with the first acting as the drive shaft, the other two as output shafts.
In the next step, the user specifies the x- and y-coordinates of the pulleys, the pulley types (depending on the belt: toothed, V or flat), the rotational direction (clockwise or counterclockwise), the number of teeth and the speed of the drive shaft. The following are input:
Pulley | x-coordinates | y-coordinates | Speed | No. of teeth | External diameter | Rotational direction |
0 (drive shaft) |
|
| 1,500 rpm | 56 |
| Counterclockwise |
1 (output shaft) | 300 mm | 50 mm |
| 28 |
| Counterclockwise |
2 | 200 mm | 50 mm |
| 28 |
| Clockwise |
Note: The back of the belt runs over the second output shaft; accordingly, this rotates clockwise rather than counterclockwise.
Based on this geometry data, Conti Professional calculates that the required belt has to have a length of 1014.63 mm. At the same time, the software issues an error message: Since the Synchrotwin CXP has a tooth pitch of 8 mm, the belt length must be divisible by 8. To complete the successful design of the oil pump drive, however, the user can assign a tension take-up range to the drive shaft which, in this case, is also operating as the tension pulley. If a tolerance of 30 mm in both positive and negative directions on the x- and y-axes is allowed and Conti Professional then calculates the tension pulley algorithm, the resulting belt length is 960 mm – a standard size in Continental’s product range. “That would be an ideal solution in this case because using belts from the standard range saves costs while at the same time ensuring a high level of availability,” says Vogel.
In addition to calculating the drive, the software can also visualize it. If required, the user can change the pulley position in the visualization via Drag & Drop, after which the geometry data is automatically updated.
Determine performance data
The user can now specify the output data for the oil pump drive. The two drive shafts are known to have a torque of 35 Nm acting on them. Conti Professional calculates all the other data on power outputs, torques and effective pulls and automatically adds it.
Pulley | P (power output) | Md (torque) | Fu (effective pull) |
0 (drive shaft) | 22.00 kW | 140.00 Nm | 1832 N |
1 (output shaft) | 11.00 kW | 35.00 Nm | 916 N |
2 (output shaft) | 11.00 kW | 35.00 Nm | 916 N |
Note: The output shaft torque is the only figure specified by the user. All the other performance data is calculated and added by Conti Professional.
The user then has to input the service factor and the operating conditions. A medium load is to be expected with an oil pump drive. The other user-definable operating conditions are constant load, frequent load changes and high impact loads. The drive shaft torque at 140 Nm is the drive’s operating point at the same time. The belt has to be capable of permanently withstanding this torque. By specifying 1.6, the user has opted for a relatively high service factor, which has a positive impact on the belt’s operational reliability.
Result in detail
The user can now have an interim result displayed which shows the belt width, overall service factor, effective pull, strand force, initial tension and overall power rating of the system. The energy cost calculator could be used to allow the user to compare the newly designed system with a previously used one and see the energy consumption, energy costs and annual savings.
In the final report, the user is given a detailed overview of the design of the oil pump drive in which the data from the preceding steps is summarized – from the belt to the pulley and system geometry through to the tension check. The drive is also visualized again. “Conti Professional can also export the final report as a PDF file and generate a data sheet for the belt used,” says Vogel. “These documents can be downloaded so that they can, for example, be forwarded to a customer. The project data, on the other hand, is stored in the software. The user can access it at any time and even share it with other registered users.”
Conti Professional therefore offers a wide range of functions and also the capability of designing almost the entire Continental belt portfolio. The software is available in ten languages and is distributed throughout the world. “Conti Professional is a very powerful tool with intuitive operation,” says the application engineer. “Some 3,500 users from almost 90 countries are already using Conti Professional. We hope to see that number grow further still – because we’re continually incorporating new features to make it even more useful to our customers.”
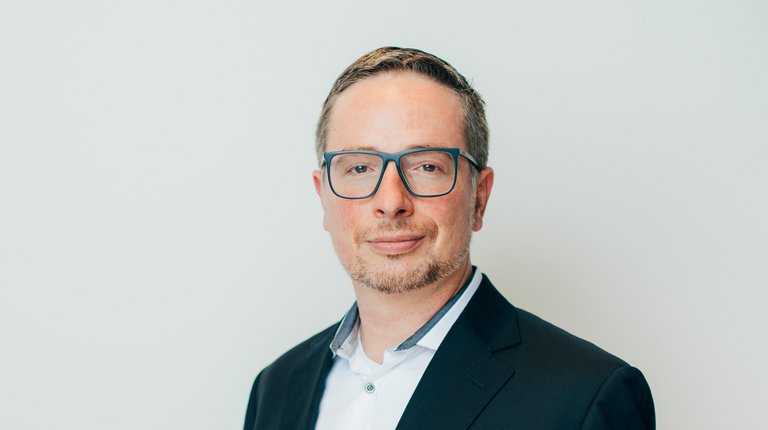
Sébastien Bonset
Media & PR Manager, Media Coordination APAC
ContiTech