New Perspectives through Factory Training
From June 1st to July 29th, we worked at our factory in Hamakita (Japan) as part of our J.DRIVE trainee program. Before the start I heard that Continental has strong interest in”Industry 4.0″ (every machine & products are connected). I could’t imagine such a “smart” factory, but I saw it in Hamakita. Most processes are automated and all data is managed in a cloud. This article is a report about my two months in this “smart” factory.
Job description
Products made at the factory are electric-brake-system (EBS) modules from our Business Unit Vehicle Dynamics (BU VED). We are split into Industrial Engineering (IE) and Quality Assurance (QA).
- IE controls the machines at the production line and improves them
- QA analyzes the products which were rejected by the automated production line and reduces the reject rate
My job at QA was to improve the reject rate based on data analysis of the process that causes the rejects. Although the task was “only” data analysis, I should learn the detail of each process to understand the reason of rejects. The final goal is not the analysis itself, but the improvement of the reject rate. Like this I had to consider the solutions from mechanical / electrical aspects. That is a difficult but interesting aspect of this work.
Communication creates “Trust”
Another interesting thing in the factory training is communication with colleagues at QA. They are friendly and answering my questions anytime even if they are busy. Some colleagues are younger than us, but their knowledge and experience is bigger. Especially their attitude for newcomers like us is brilliant. They don’t forget that we are all working “For One Another”, and that creates “Trust” I think. I would like to copy their mindset, and keep up efforts of communication when I am the experienced guy.
Sports connect people
As I wrote in the past post, the strongest tool to connect people is sport, and I experienced the truth again at Hamakita.
When I played tennis with colleagues at Yokohama, I talked about factory training at Hamakita. Then Ogino-san from Passive Safety & Sensorics (PSS) introduced me to Nakamura-san who is the head of QA to me. Thanks to Ogino-san, I could communicate with Nakamura-san smoothly from the start, and finally we played tennis together!!
Besides that, we played many sports; bowling, basketball, and airsoft with young colleagues. At the factory, our conversation should be related to our job, so we planned such sport events to build better relationship. This purpose is achieved, and now we still keep in touch with them. Communication across functions is necessary to produce better products. I would like to keep this mind until traffic accidents disappear worldwide.
That’s all for this time. Thanks for nice guys at Hamakita factory!!
This article was written by our employee.
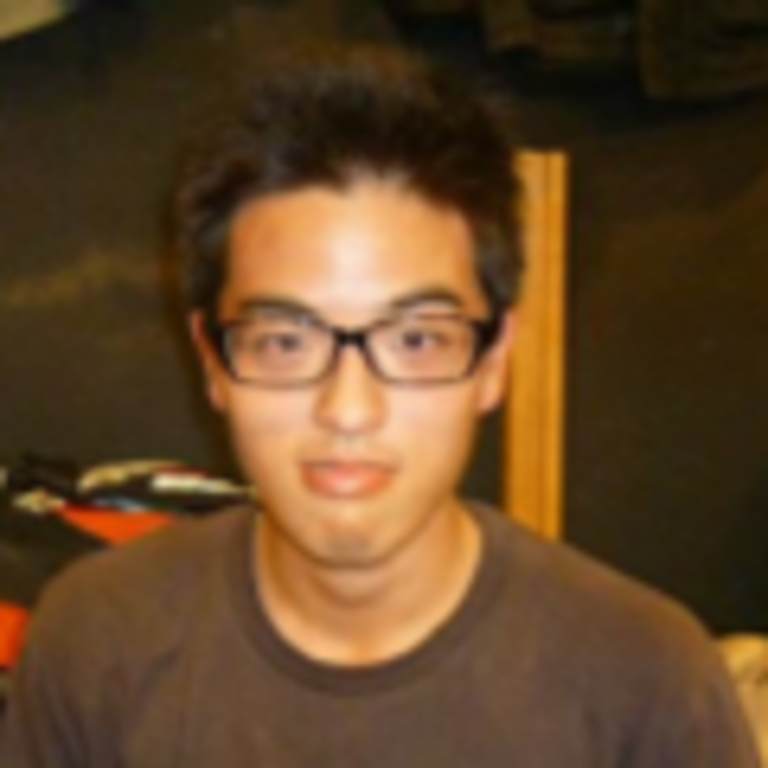
Nobuto Yoshimura