LogiMAT 2024
Continental optimizes intralogistics with robots, tires and digital solutions
Continental has presented its broad product and service portfolio for the intralogistics industry at LogiMAT 2024 and demonstrated how innovative technology solutions can help to master the challenges of the future. At LogiMAT, the international trade fair for intralogistics solutions and process management we have been showcasing advanced solutions for intralogistics.
Contacts for the media
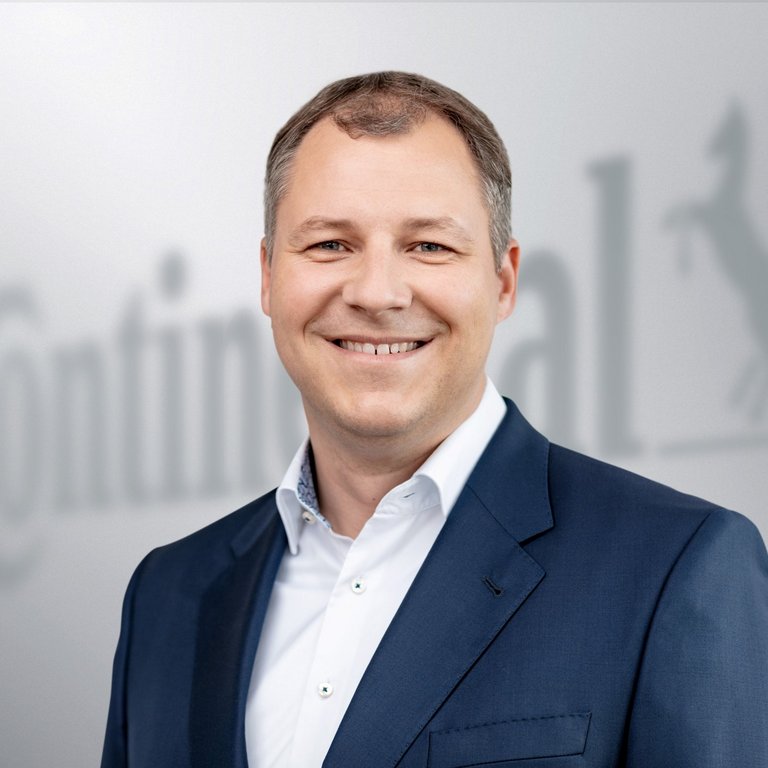
Sören Pinkow
Media Spokesperson Autonomous Mobility and Commercial Vehicles
Continental Automotive
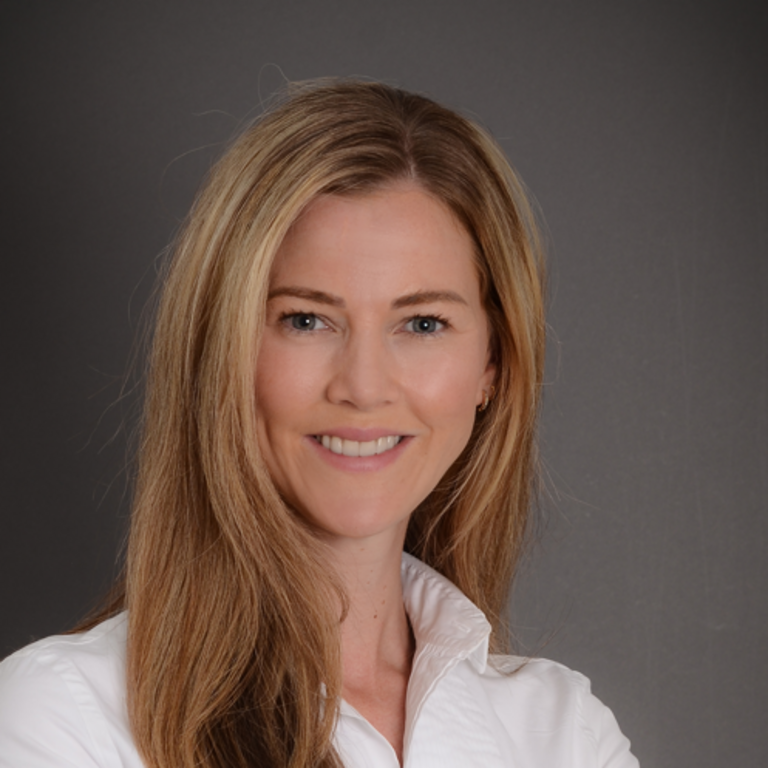
Valerie Libercka
Media Spokesperson Smart Mobility
Continental Automotive
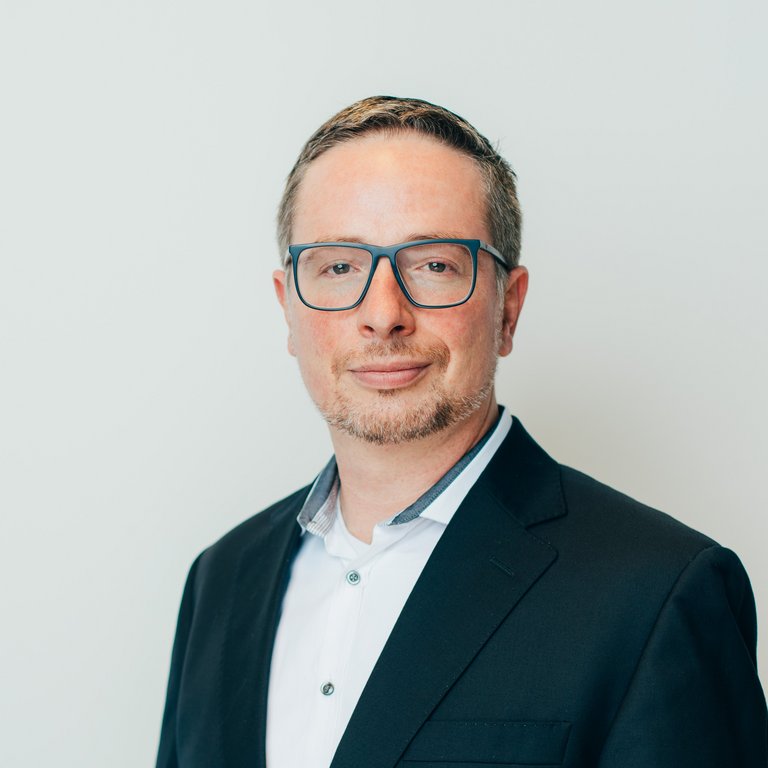
Sébastien Bonset
Media & PR Manager, Media Coordination APAC
ContiTech
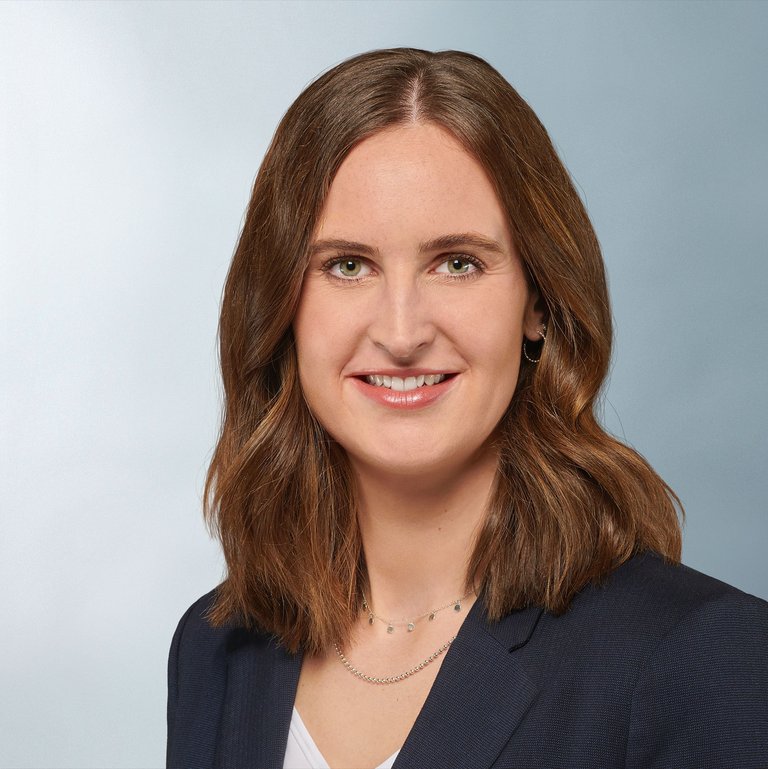
Julia Reinhold
Communications Manager Commercial Specialty Tires
Specialty Tires
Continental Tires
- +49 511 938-2570
Highly efficient. Down to earth. Attention to details.
Autonomous transport robots optimize material transport on the shop floor
Continental is presenting an autonomous transport vehicle developed in-house that increases efficiency in production. The autonomous mobile robots (AMR) automate the material flow in production plants, warehouses and logistics centers. The AMRs have a load capacity of 1.2 tons and perform all tasks completely autonomously. Customers can currently choose between the three use cases Cart, Top Roller and Load Module. Continental offers an optional intelligent fleet management software, Fleet Master Control, to control the AMRs.
Cart
Thanks to its integrated lifting function, the AMR can drive autonomously under trolleys, lift them, and transport them to their destination. With its ultra-compact design and payload of up to 1,200 kilograms, the AMR performs all work completely autonomously. The maximum speed of the robot is up to two meters per second.
Top Roller
If an interlinking of the existing conveyor system with the AMR material flow is planned, Continental's AMR is also a good choice in this application area thanks to a partnership with ROEQ. Coordinated with each other, the automated pick-up and delivery of or to roller conveyors such as high-bay warehouses or production lines becomes the absolute standard. The safety of man, machine and goods is guaranteed by the robot's 360-degree environment detection.
Load Module
The goods are automatically approached from defined transfer stations, lifted out of the station, and transported to their destination. Basically, designed for transporting pallets, important features such as 360-degree obstacle detection complement safety during pickup, transport, unloading, transfer, or independent approach to the loading station. Orchestrated in a defined infrastructure, maximum efficiency is now just a question of the right (system) setting.
A revolution in material flow automation: Find out more about the Continental Mobile Robot
Heavy-duty timing belts for automated storage and retrieval systems
High-bay warehouses are the beating heart of many logistics processes. Filling them and removing goods from them effectively is a major challenge that is increasingly being met by automated storage and retrieval systems with belt drives. As key elements in intralogistics processes, they position goods quickly and precisely. Together with a partner, Continental has developed a new drive technology that is based on the principle of the block and tackle and works with a deflected belt drive. Here, a Synchrodrive timing belt demonstrates several advantages over the rope technology that is often used: minimal wear and tear, less maintenance, shorter positioning times and longer change intervals. The belt technology does not require any lubrication and has already proven beneficial in series production – under large loads as well as in the low-temperature range. Continental makes to a large proportion the compounds needed to produce the corresponding belts in-house. The belts are available in both black and white versions. The new-generation Synchrodrive timing belts are "closed" belts. With this technology, no tensile cords are exposed. This enables a longer service life even under the most demanding conditions, such as maximum load or outdoor conditions. Wetness or humidity indoors and outdoors cannot harm the belt.
Efficient solutions for smooth material logistics: Find out more about material handling with Continental
Tires: Digital tire monitoring saves fuel and reduces downtime
The demands placed on vehicles in intralogistics are high. They have to do their job even more efficiently, lift higher loads and cover longer distances with higher turnaround times than before. At LogiMAT 2024, Continental will be showcasing its solutions for rolling logistics: in addition to its solid tire solutions from the Continental, General Tire and Barum brands, the manufacturer will also be presenting its pneumatic tire portfolio and digital solutions. Whether for forklift trucks, tractors, heavy-duty transportation, ground vehicles at airports or trailer vehicles. Optimally inflated tires can save around one percent fuel compared to a tire that is ten percent underinflated. The ContiConnect digital tire management system, which the company is presenting at LogiMAT, thus eliminates the need for time-consuming manual checks. This is because the sensors in the pneumatic tires transmit data about the air pressure and temperature in real time and can inform the driver via a warning system if the tire pressure is too low or there is a risk of overheating. They contribute to predictive maintenance and ensure greater safety and efficiency in operation. Another advantage: the Bluetooth-enabled sensors make it possible to read tire data directly from the vehicle via mobile devices such as smartphones.
Continental's solid tire range caters to a wide variety of customer needs with different requirements and is particularly focused on sustainability with its SC20+. The new Super Elastic solid tires produced at the Continental tire plant in Korbach, Germany, contain around 60 percent renewable and recycled materials.
Find out more about Continental tires for the logistics and port industry
SHAPING CHANGE TOGETHER:
International Trade Show for Intralogistics Solutions and Process Management LogiMAT