VDA Logistics Award 2022 – Continental Honored for Industry 4.0 Initiative
- Continental's winning concept increases efficiency and transparency of the supply chain
- Sustainable system of eleven standardized technology solutions is already digitalizing Continental's internal material flow at 38 locations worldwide
- VDA President Hildegard Müller praises "impressive innovative strength of the automotive industry"
Regensburg/Frankfurt, Germany, 19 May 2022. As part of the Forum Automotive Logistics (FAL) in Friedrichshafen, Germany, the German Association of the Automotive Industry (Verband der Automobilindustrie , VDA) honored the technology company Continental with the VDA Logistics Award 2022. Continental has received the highest award for the holistically sustainable concept "Touchless Material Flow – internal supply chains become smart". Especially in times of increasing geopolitical uncertainty, volatile developments and advancing digitalization, the system makes a significant contribution to achieving the sustainability goals, reduces manual activities in the internal material flow of the supply chains and improves process efficiency and ergonomics for employees. Every year, the VDA Logistics Award honors outstanding logistics solutions that serve as role models for other companies in the automotive industry.
Hildegard Müller, President of the German Association of the Automotive Industry (VDA), emphasized at the award ceremony on May 18, 2022: "The VDA Logistics Award is the 'Oscar' of the automotive logistics industry – and every year it once again demonstrates the impressive innovative strength of the automotive industry. The numerous applications are a clear sign of the attractiveness of this award – and also of the creativity and entrepreneurial spirit of our industry. Congratulations to the winners!"
"My warm thanks go to the entire Continental team, who is showing extraordinary performance in the current crises.Together, despite these operational challenges, we have succeeded in advancing digitalization in the internal material flow," says Jürgen Braunstetter, Head of Supply Chain Management Automotive at Continental. "Through standardization and connectivity of all implemented Industry 4.0 solutions, we have established a holistic, efficient and flexible system for our plants, which the VDA has now even awarded. With this comprehensive concept, our team has made a major contribution to the implementation of the vision of ‘Touchless Material Flow’."
Efficient and sustainable: Digitalization of the internal material flow
Continental's concept convinced the jury with a fully sustainable approach consisting of eleven standardized technology solutions that further advance the digitalization of supply chains and the internal material flow. Connectivity and integration are at the forefront of the development and implementation of all individual solutions.
Continental's connected solutions are already being used in 38 of the technology company's plants and include a sorting and booking station that almost completely automates the incoming goods processes. With another solution, the specially developed material replenishment control software, all the necessary components are requested from the warehouse based on inventory and demand. Today, more than 240 production lines for surface-mounted devices and final assembly are connected to this software. After removal of stock, the components will be delivered just-in-time with more than 300 autonomous mobile robots (AMR) to these lines in the Continental plants. A holistic fleet manager also coordinates and analyzes the flow of goods and controls all manual and automated transport systems. In addition, more than 1,600 collaborative robots, or cobots for short, are used in the internal supply chain and in the production area. This results in financial savings opportunities and a potential reduction in inventory on the production line. In addition, generated data and AI-based optimizations in real time lead to an effective internal supply chain. Overall, the concept contributes to the achievement of sustainability goals and better process efficiency, reduces manual activities in the internal material flow and thus improves ergonomics for the employees.
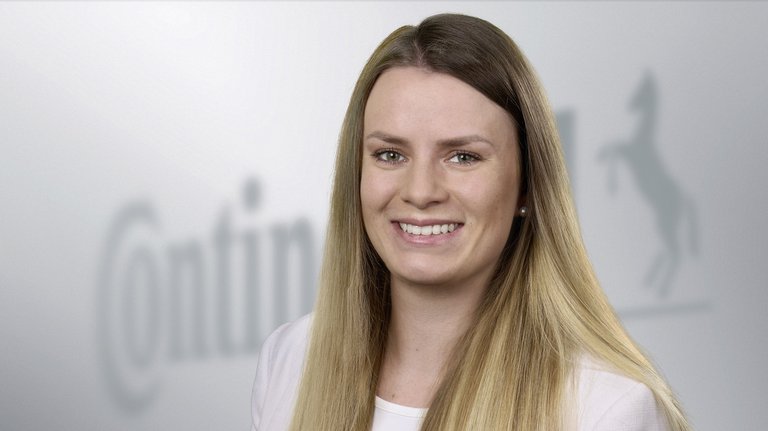
Jennifer Weyrich
Media Spokesperson and Topic Manager Autonomous Mobility
Continental Automotive
(On maternity leave)