ContiTech Presents Highly Accurate Measurement Technology and the Strongest Steel Cord Conveyor Belt in the World
- Predictive maintenance: digital monitoring system for heavy-duty steel cord conveyor belts
- Strongest volume-produced conveyor belt in the world
Hanover, April 2017. When every minute counts, ContiTech offers the right solution for the faultless use of conveyor belts. The Hannover Messe trade fair will see the international industrial partner present the new Conti MultiProtect – a permanently installable and digitally connected monitoring system for steel cord conveyor belts. The new software solution, which is intelligent and saves both costs and time, supports operators in maintaining and servicing their systems. In addition, with the Stahlcord ST 10 000, ContiTech will be presenting the strongest volume-produced conveyor belt in the world.
Belts running smoothly thanks to intelligent software solution
Conveyor belts keep the globalized cycle of industry moving. From ore, pit coal, rough rubble, glowing hot slag and goods containing oil or grease to rare earths for up-to-date electronics and high-tech tools – conveyor belts take on anything that needs to be quickly and safely transported. In harsh working conditions, they cope with distances of several kilometers and height differences of up to 700 meters. And everywhere where top-quality and reliability is important, where service and sophisticated solutions are sought-after, ContiTech is there in a flash with intelligent software solutions and extremely high-performance conveyor belts.
If a belt system experiences an extended period of downtime due to damage, the entire production chain frequently collapses. This in turn results in considerable sales losses for the operators.
Preventative systems help conveyor belt systems to run cost-effectively and without any problems in the long term, even when subjected to high loads. An example of this is ContiTech’s innovative electronic monitoring system, with which the exact status of conveyor belts can be determined at any time and therefore enables prompt repairs with short periods of downtime.
Predictive maintenance: avoiding downtime and reducing maintenance costs
Serious damage, such as longitudinal slitting on conveyor belts, frequently happens in systems where copper, iron or sharp rocks bounce along the surface of the belt, causing strain and damage. To identify the extent and position of such damage, intensive servicing is necessary. Up to now, technicians, referred to as “belt runners”, have had to evaluate the state of conveyor belts individually while they have been running at a reduced operating speed or when they have come to a stop. This process means high time, personnel and cost expenditure. “With our own software solution, Conti MultiProtect, damage to conveyor belts can be recognized early on while the system is running. This allows carcass repairs to be scheduled preventively in good time, avoiding long downtimes and reducing maintenance costs,” explains ContiTech application engineer Patrick Raffler. The monitoring system is also able to record the condition of the joints and identify damaged spots within the carcass.
Conti MultiProtect uses a magnet system that works in combination with rip inserts that are embedded in conveyor belts at regular intervals of approximately 50–200 meters. Rip inserts are checked for possible longitudinal slitting by means of their characteristic magnetic fields. Using RFID (radio-frequency identification) chips, ContiTech has optimized localization of longitudinal slitting on the belt. By means of a special sensor application, the rip insert function can also monitor the rotation of tube conveyors. The user-friendly system sends the easily interpreted data to the screen, displaying the damage to the conveyor belt in an understandable format. Furthermore, touchscreen displays ensure that the system is easy to operate. If desired, Conti Protect systems can also be remotely maintained worldwide by experienced ContiTech engineers.
In addition to Conti MultiProtect, ContiTech offers other intelligent systems: Conti Protect monitoring systems protect conveyor belt systems against major damage. They thereby make an important contribution to increasing operational dependability, thanks to a reduction in damage-related idle times.
On the other hand, Conti Inspect systems supply data that can be used to make reliable prognoses regarding the remaining service life of the conveyor belt. This allows operators to better estimate investment costs earlier.
The strongest volume-produced conveyor belt in the world
The latest high-strength steel cord conveyor belt by ContiTech for bulk haulage and copper ore operations, the Stahlcord ST 10 000, is predestined to overcome large differences in height and long distances. Stahlcord conveyor belts have a layer of particularly stable steel cords in a planar arrangement and embedded in rubber. The high-performance conveyor belt also impresses with a high level of resistance to impact and rips thanks to the use of transverse reinforcements. These guarantee more safety and stability and protect against impact breaks and damage to the steel cords. In addition, with the Stahlcord ST 10 000, system operators can also reduce expensive transfer points and drive stations. ContiTech offers the steel cord conveyor belt in varying cover qualities, depending on requirements, for use in both aboveground and underground operations. Customers can choose between flame resistant or energy-saving properties.
Through the use of high-strength steel cords of minimal diameter, a two-meter-wide ST 10 000 is able to resist traction of up to 2,000 metrics tons. ContiTech proved dynamic connection time stability of a significant 60 percent in tests. In order to minimize vulnerable joints, ContiTech supplies the Stahlcord ST 10 000 on large, length-optimized reels. “With the ST 10 000 steel cord, we set new standards. Our customers benefit from the high capacity and safe operation with low idle time even on heavy-duty conveyor belts,” says Harald Koch, head of development at ContiTech.
Operators who rely on solutions from the conveyor belt manufacturer also enjoy many other advantages: “Our customers receive everything from one source – from technical advice, extensive planning and engineer-driven development to manufacturing and the delivery, installation and commissioning of conveyor belts and components. Maintenance and monitoring of the belt round off the whole package: This is all perfectly tuned to achieve the best possible operation and highest level of customer benefit,” emphasizes Raffler. With expert advice, round-the-clock support for emergencies and an extensive service offer that covers every special case, ContiTech meets requirements for the highest levels of quality, safety and flexibility. The company’s focus is maximum benefit for the customer through intelligent complete solutions.
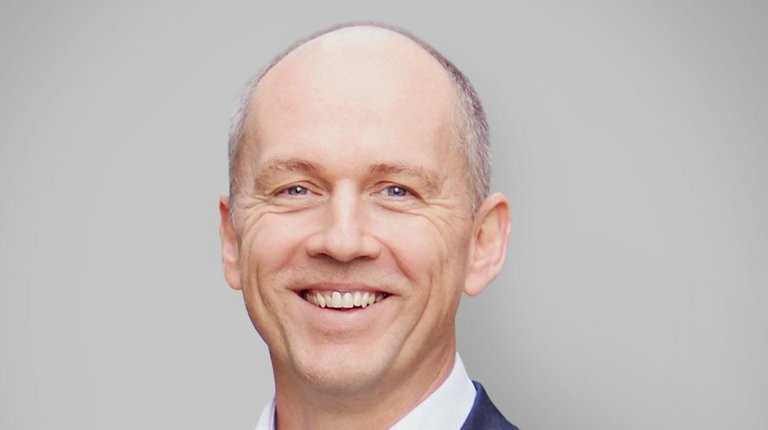
Wolfgang Reinert
Head of Media & Public Relations
ContiTech
- Insulation System with Multiple Potential Smart Applications
- Radar Sensor for Intelligent Solutions in Industrial Applications
- Intelligent Drive Belts Enable Preventive Maintenance and Reduced Maintenance Outlay
- ContiTech Presents Highly Accurate Measurement Technology and the Strongest Steel Cord Conveyor Belt in the World
- Conti Professional: New Functionalities Added to Drive Design Software
- ContiTech Further Develops App for Mobile Vibration Analysis
- Hannover Messe: ContiTech Rewards Reliable Partners